Handling Supply Chain Volatility in the Logistics Industry
February 24, 2022
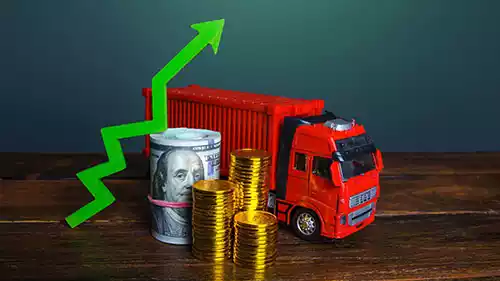
“We’ve been waiting for the other shoe to drop, and I think that’s what we’re seeing now,” says Wendy Workman, Senior Director of Supply Chain with SK Food Group when describing recent volatility in the transport industry. In her view, current conditions result from problems that have been developing for some time.
Labor challenges and poor planning are among the major contributing factors, which should come as no surprise to those who follow industry trends closely. When the pandemic struck, the effects of poor business practices that had previously flown under the radar finally caught up to the industry at large.
What were some of warning signs that business owners could have used to forecast disruptions on the horizon? Watch the podcast to hear what our guests had to say.
Since around the year 2000, the transportation industry has changed dramatically. The advent of the internet led to many new opportunities, transforming communication in a field that had long been organized around word of mouth and handshake deals. These changes allowed more companies to enter the game on a wider scale, diminishing some of the personal touch that had once been key to business relationships. While companies scrambled to adapt to these new dynamics, other challenges such as disruptions following Hurricane Katrina further complicated matters in the early 2000s. These difficulties and many others highlighted the underlying volatility of modern logistics that would later be exposed by conditions caused by the pandemic.
Following the pandemic, the shortfalls of widely adopted “just-in-time” practices were made clear. Even with the breakneck pace of modern logistics, managing a successful operation depends on more than providing the fastest, cheapest option.
“There are two elements to running good logistics,” says Todd Burk, Vice President/General Manager of Icon Foods. “One is the cost component. Cost is important, but it’s not exclusive. The other is continuity of service, which is the service element. You have to balance both of those so you’re getting the best service at the lowest cost.”
What is the best way to manage cost and supply? The answer to this question and more can be found within the full episode.
For brokers, personal connections are still the key to success for doing business in the post-pandemic age. “It starts with the relationship, and it starts with respect,” says John Mahle, host of the Stay In Your Lane Podcast and Senior Sales Executive at Triple T Transport. “The lowest cost at the best value is what we’re here to provide. It’s the showcase for how we operate.”
Still, a broad view of the industry demonstrates that there is much work to be done to repair and maintain healthy logistics nationwide and beyond.
“If we don’t make some corrections quickly, the volatility that we are seeing now is only going to worsen,” says Wendy. “I’m not sure how much more the market can sustain.”
What can be done to mitigate issues of volatility for ourselves and our industry partners? What can shippers do to get back to more normalized rates? For all this and more, watch the first episode of the Stay In Your Lane Podcast. Stay tuned for new episodes each month with valuable perspectives from both carriers AND the suppliers you won’t find anywhere else.
In the first episode of the Stay in Your Lane Podcast, Wendy Workman, Senior Director of Supply Chain with SK Food Group, and Todd Burk, Vice President/General Manager of Icon Foods join Triple T’s John Mahle to discuss some of the largest challenges in the logistics industry today. Among many topics, our guests shared insights into the recent volatility of freight costs and factors that have contributed to the supply chain issues that we now see.