Common sense cost savings in transport procurement
August 31, 2022
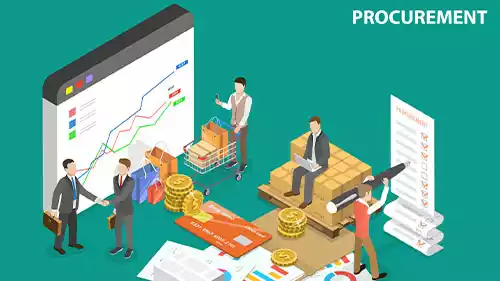
With skyrocketing interest rates, high fuel prices, rampant inflation, and looming recession, has the role of procurement in the transport industry changed?
Historically, the performance of procurement professionals has been measured based on cost savings from one period to the next. But savings alone is hardly enough to go by. Isolating and tracking other specified cost metrics will help to show important indicators such as supplier efficiency, which can also be used to track success when it comes to procurement.
“Procurement is about more than just low cost,” explains industry veteran Joe Lombardo of the consulting firm Ege Avenue associates. “If you look at just low cost, you’re going to sub optimize some other part of the supplier value chain.”
What’s the secret to long-term cost savings in procurement? Learn more by watching the Stay In Your Lane Podcast.
Factors such as on-time delivery, completeness of deliveries, and sustainability all play heavily into the picture of success for procurement operations. Total delivered costs (TDC) have become a new standard for measuring value, especially in light of recent inflation.
For larger businesses, procurement teams have more tools at their disposal to combat uncertain economic conditions—some of which are not for the faint of heart.
“Large companies—Nestle, Unilever, Kraft-Heinz—one of the tools that they have is hedging the price of commodities,” Lombardo explains. “At Nestle, one of the things we hedged on was home heating oil, which is basically the same as diesel.”
Buying futures based on where they believed the price would move, a company like Nestle could hope to save a fortune in fuel costs. Obviously, the inherent risk of such a tricky fiscal maneuver would place this tactic outside of the acceptable range for most smaller operations. For large companies more capable of absorbing such risks, hedging is a valuable tool for cost savings.
How has the role of procurement changed since the onset of the pandemic? Find out in the latest episode of the Stay In Your Lane Podcast.
Again, cost savings alone cannot be used to define success or failure. It must be considered alongside many variables from across the supply chain. An overreliance on reducing costs can often lead to shortfalls in other areas. For example, reducing costs in transportation or warehousing might be achieved by cutting corners with operators. An underperforming operator could then cause late deliveries, which in turn causes late fees and lost business through damaged relationships. Suddenly, your cost savings efforts have incurred unforeseen costs of their own.
Cost increases in the transport industry are unavoidable to an extent. Instead of chasing savings at all costs, a more responsible approach is to cultivate consistency and balance with the factors in the supply chain that you can control. On time delivery, strong customer service, retaining quality carriers: elements such as these can help maintain business through trying times and create organic opportunities for cost savings.
For a supply chain partner you can count on for consistency and superior service, trust the 3PL professionals at Triple T Transport. Our decades of expertise in transport and logistics will help you keep costs low and maintain the strong business relationships you need to succeed. Click here to learn more about our award-winning brokerage services.